Plenary Speakers
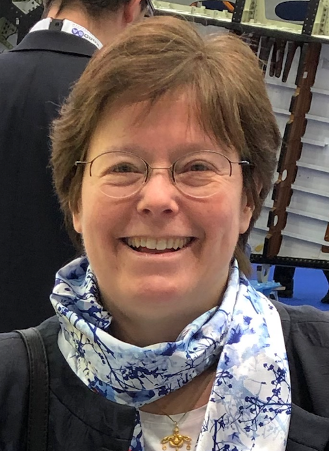
Pr Véronique Michaud
Pr Véronique Michaud
Laboratory for Processing of Advanced Composites
Ecole Polytechnique Fédérale de Lausanne- Switzerland
Biography:
Pr Véronique Michaud is currently Associate Professor, head of the Laboratory for Processing of Advanced Composites and Associate Dean of Engineering for Education, at the Ecole Polytechnique Fédérale de Lausanne, in Switzerland. She graduated in 1987 from Ecole des Mines in Paris with an engineering degree, in 1991 from MIT with a PhD in Materials Engineering, and obtained a Research Habilitation from INPG in France in 1994. After a post-doctoral research stay at MIT, she spent 3 years at Ecole Centrale in Paris for teaching and research in the Laboratory for Materials, Structures and Soils Mechanics, before joining EPFL in 1997. Her fields of research address fundamental aspects of composite materials processing, often including economic and environmental aspects to lower the overall product footprint, as well as the development of smart materials and structures including self-healing, shape and vibration control and tailored damping. She is the author of more than 350 publications, out of which about 170 in peer-reviewed journals, and several patents. She is also the co-founder of the start-up CompPair Technologies SA, which was created in 2020.
Title:
Energy efficient thermoset composite manufacturing processes.
Abstract:
When manufacturing fiber reinforced composite materials, either with a thermoset or a thermoplastic resin, external energy is generally required to heat-up the molds and cure or melt the matrix material to produce the final part. We recently explored frontal polymerization as an alternative to oven cure for epoxy-based resins, which has the potential to bring unprecedented reductions in energy demand and process time. Production of epoxy-based fiber reinforced polymer parts with high fiber volume content is however difficult with this process as the heat sink created by the fibers and the mold overcomes the heat output of the chemical reaction, thus preventing front propagation. We thus developed a novel self-catalyzed frontal polymerization manufacturing method using well insulated molds and the integration of thin resin channels in thermal contact with the composite stack to produce high fiber volume fraction polymer composites without the need for a continuous energy input. Frontal polymerization inside the resin channel proceeds faster and preheats the fabric stack, thus catalyzing the process. Parts with up to 60% fiber content were successfully produced. We also explored the use of fillers added within the resin channels to tailor the frontal polymerization process kinetics. The parts have a higher glass transition temperature than those produced in a conventional oven, and comparable mechanical properties while energy consumption is reduced by over 99.5%.
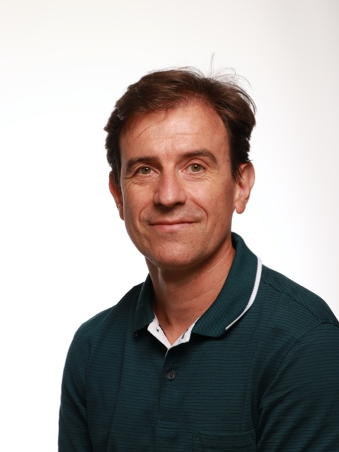
Pr Eric Coatanea
Pr Eric Coatanea
Manufacturing and Systems Engineering Group
Tampere University – Finland
Biography:
Pr Eric Coatanéa received his BS degree in Mechanical Engineering from the University of Western Brittany, Brest, France in 1990, his MS degree in Mechanical Engineering from INSA Toulouse, France in 1993 and his teaching certificate from Ecole Normale Supérieure de Cachan, France in 1994.
He worked for 11 years as a lecturer in manufacturing engineering at the University of Western Brittany, Brest, France, while remaining active in athletics. He started joint doctoral studies in 2002 and received his joint PhD in Mechanical Engineering from the Helsinki University of Technology, Finland (now Aalto University) and the University of West Brittany, Brest, France in 2005.
He is a tenured professor of manufacturing engineering and systems engineering at the Faculty of Engineering and Natural Sciences, Tampere University, Finland. He was a Marie Curie fellow from 2005 to 2007. He has held visiting professorships at several universities. He leads the Manufacturing Research Group at Tampere University. His research interests include design and manufacturing activities, engineering design, causal inference, systems thinking and systems engineering. In particular, the research focuses on the early integration of simulation and decision support tools in the early design phases
Title:
Graph-based Modeling for Integrated Design and Manufacturing: What could be the benefits of a graph-based approach for manufacturing?
Abstract:
The process of designing and producing artefacts is characterized by a sharp increase in complexity. Factors contributing to that transformation are the increasing integration of standards and specifications, the ubiquitous presence of cyber and electronics, the massive integration of sensors and the combination of systems in the form of systems of systems. Therefore, humans are overwhelmed by the cognitive load associated with the complexity and the required acceleration of processes and actions. One viable way forward can be the increase of human-machine collaboration. This presentation introduces a graph-based modelling framework supporting this deeper human-machine cooperation. The framework promotes the principles of explicability and parsimony. The talk summarizes the principles behind the framework, presents the domains of applications and exemplifies the practical usage of the framework named DACM (Dimensional Analysis Conceptual Modelling) in manufacturing and design.
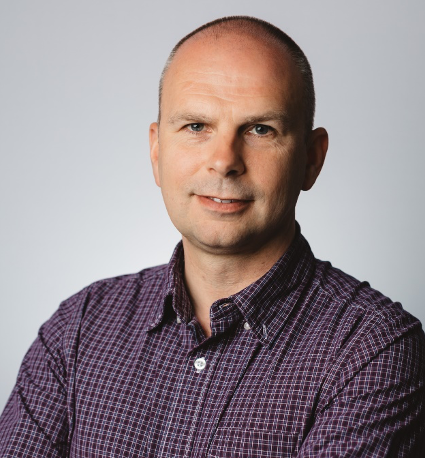
Pr Gary Menary
Pr Gary Menary
School of Mechanical and Aerospace Engineering
Advanced Materials and Processing
Material and Advanced Technologies for Healthcare
Biography:
Gary Menary is a Professor of Polymer Mechanics at Queen’s University of Belfast. He has a bachelor’s degree in mechanical engineering, a master’s degree in Computer Aided Engineering and in 2001 graduated with a PhD focused on developing forming simulations for stretch blow moulding of PET bottles.
Prof Menary has 27 years of experience of research on modelling and simulation of polymer processing applied to the packaging and medical device industries., He has led several UK, EU and industrial projects and has over 100 journal publications. He is co-founder of a spinout company Blow Moulding Technologies which has resulted in significant impact within the packaging industry.
Prof Menary is on the editorial board of the International Journal of Materiel Forming. He has been on the Board of Directors of the European Association of Material Forming (ESAFORM) since 2006 and was the ESAFORM conference chairman in 2011. He is currently President of the Jury for the award of the ESAFORM scientific prize and Lionel Fourment PhD Prize for industrial research.
Title:
Advancing Sustainability in PET Bottle Forming through Simulation.
Abstract:
In a world where sustainability is paramount, the packaging industry faces the challenge of reducing its environmental footprint. PET (Polyethylene terephthalate) bottles are a ubiquitous choice, but their production and impact on the environment are under scrutiny. This talk delves into innovative solutions for enhancing the sustainability of PET bottle packaging through the power of material forming simulations.
Over the span of 30 years, this research has explored non-linear viscoelastic constitutive modelling, in-process measurements, forming simulations, customised material characterization techniques, experimental mechanics (digital image correlation), and the integration of machine learning for optimization.
This presentation will demonstrate how the integration of these technologies is key to obtaining accurate forming simulations and will highlight the industrial relevance and impact of the work. It will explore how simulations have enabled innovation in PET bottle packaging, reducing material waste, energy consumption, and environmental impact. The focus will be on the transition from fundamental science to practical applications, demonstrating the potential for sustainable change in the world of packaging.
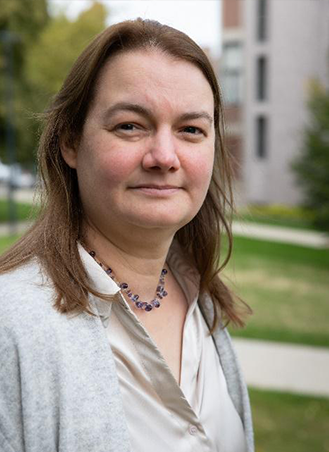
Pr Aude Simar
Pr Aude Simar
Institute of Mechanics, Materials and Civil Engineering
Université catholique de Louvain, Belgium
Biography:
After her Mechanical Engineering Degree at the University catholique de Louvain (UCLouvain) in Belgium in 2002, Aude Simar obtained a Ph.D. from the same university in 2006 with research related to friction stir welding in aluminum alloys. She was a post-doctoral fellow for 1.5 years at the University of California at Berkeley (UCB) in the USA. After returning to UCLouvain, she joined the academic staff of the university in 2013. In 2016, she received an ERC starting Grant (ALUFIX) with the aim to mitigate and heal damage in aluminum alloys. Pr. Simar is known for her contributions to the understanding of damage of metallic materials, additive manufacturing and friction stir based processed for aluminum alloys and dissimilar welding. She supervised 40 researchers working on these various topics. She is part of the editorial board of “Materials Characterization” and “International Materials Review”.
Title:
Friction stir allows much more than welding: enhancing mechanical properties of aluminum alloys, make them healable or as an additive manufacturing process.
Abstract:
Friction stir welding is an established solid-state welding process for assembling aluminum alloys. It may be adapted to process materials including manufacturing metal matrix composites, improving the ductility of alloys or for additive manufacturing. Friction stir processing can be used to integrate fast-diffusing atoms at a high volume fraction in aluminum to favor its healing potential. The process can also significantly improve the fatigue life of Laser Powder Bed Fusion aluminum alloys or improve the ductility of 7xxx alloys without any loss in strength. A revisited process has also the ability to additive manufacture parts with these high-quality standards. The enhanced mechanical properties compared to cast or even wrought alloys is associated to the refined microstructure following severe plastic deformation.